Water footprint of the banana industry
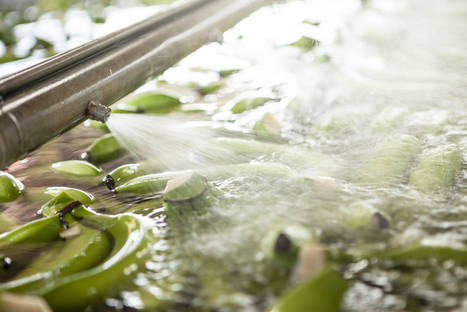
Agriculture uses 70% of the world’s freshwater drawn from aquifers, streams and lakes. As a result of the growing population global food production is expected to increase by 70% by 2050, having a direct impact on water resources1. Banana plantations require an ample and frequent water supply, and deficits could adversely affect crop growth and yields. Being a long duration crop, the total water-per year requirements are high, varying between 1 200 mm in the humid tropics to 2 200 in the dry tropics.
Given the importance of irrigation and drainage in the banana production process, water consumption and pollution has long been a topic of interest for the industry, particularly since consumers are more demanding with regards to the impact of the products they buy2. In the banana industry, water management practices have significantly reduced its water footprint, defined as the measure of the consumption and contamination of freshwater resources for the production of a good or service3.
Water footprint assessment
As water footprint is a relatively recent concept, few studies have been published on the topic. At the international level, a comparison of available methodologies for the quantification of environmental footprints related to the use of water resources has been developed4:
Comparison of methodologies - environmental footprints and water use
Details | Hoekstra et al, 2011 | ISO, 2014 |
Methodology denomination | The Water Footprint Assessment Manual | ISO14046:2014, Environmental management – Water footprint – Principles, requirements and guidelines |
Author | Water Footprint Network (WFN) | International Standard Organization (ISO) |
Footprint denomination | Water footprint (Spanish: “huella hídrica”) | Water footprint (Spanish: “huella de agua”) |
Footprint definition | "Volumetric measurement of water consumption and pollution" | "Metrics that quantify the possible environmental impacts related to water" |
Scope | Defines a series of criteria and procedures for the calculation of the water footprint (WFP), classified in: blue, green and grey. The blue WFP contemplates the consumptive uses of surface water and groundwater, and the green WFP those in which the source is rainwater. Grey WFP is the fresh water needed to assimilate contaminant loads. | Establishes principles, requirements and guidelines for the development and reporting of a water footprint assessment, based on the LCA, of products, processes and organizations.
|
Footprint assessment steps | (i) Definition of the objective and scope, (ii) Accounting for the water footprint, (iii) Evaluation of the sustainability of the water footprint, (iv) Formulation of the water footprint response. | (i) Definition of the objective and scope, (ii) Analysis of the water footprint inventory, (iii) Evaluation of the impact of the water footprint, (iv) Interpretation of results. |
Results | Volume of consumptive water classified by the type of source from which it is taken (blue and green WFP) and volume of fresh water required to assimilate the pollutant load (grey WFP). The volumes are given per unit of product or time according to the scope definition. | Individual value of the impact or a profile of its results. The results are given according to the functional unit defined in the scope, which is a "quantitative indicator of the performance of the process or system, which is used as reference and comparison unit”. |
Comments | This methodology was developed by professional members of the WFN partner organizations. Its application tends to be complex, so it includes a section of examples for different cases and frequently asked questions. It clarifies that WFP "is not a measure of the severity of local environmental impacts of water consumption and pollution". | Developed by the ISO / TC 207 Technical Committee of Environmental Management, and integrated by professionals from different fields and countries. A study can only be called "water footprint" if it is comprehensive (principle of integrality), that is to say if it includes all significant environmental impacts in relation to the availability and degradation of the resource. |

Steps to measure the water footprint of products, processes and organizations:
- Definition of objectives
- Definition of the scope of the evaluation (in terms of geography and time)
- Collection of data and accounting for each stage of the production process
- Calculation of the footprint
- Evaluation of the sustainability of the water footprint
- Recommendations for reducing the water footprint
In studies conducted to calculate the water footprint of banana growing and processing, impact is measured in terms of water volumes consumed and contaminated per unit of product. The results vary substantially between countries, while the WFN has found a global average water footprint of 790 m3/tonne for bananas6. The results depend on the production and processing system used, and on the water source.
Activities contributing to the banana industry water footprint
Irrigation
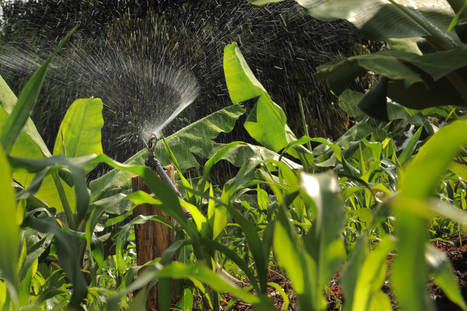
Banana cultivation demands a large and frequent water supply throughout the production cycle to ensure productivity and fruit quality7. The types of irrigation used for banana can be sub foliar spray, supra foliar spray, drip or gravity. Selection of the irrigation system depends on the availability of resources and access to technology. Aspects such as moisture retention, basic infiltration, evaporation and water balance potential also must be considered8.
Water management in banana plantations is a major issue since the rate of pumping alters groundwater and surface water with the construction of wells, irrigation pumps, canal systems and surface drainage. This affects the water balance and supply in nearby communities9. For this reason, it is necessary to implement appropriate management practices to minimize the social and environmental impact of water use.
Impact of irrigation
Studies to calculate the water footprint in large10 11 and small7 plantations have concluded that about 99% of the water footprint corresponds to the agricultural production phase. According to the WFN analysis, the corresponding percentage in blue, green or grey water footprint depends on:
- The type of irrigation: in the case of Costa Rica10, where no irrigation is needed, 100% of the water footprint is green, while in cases like Peru7, where the dependence on irrigation is high and the irrigation systems used are inefficient in terms of water utilization, 94% of the water footprint is classified as blue. There are also intermediate cases like Honduras10 or Ecuador7, with blue water footprints between 20% and 34%, since they are less dependent on irrigation, or the systems used are more efficient.
- The production system: in conventional production systems, such as in Ecuador7, the calculated grey water footprint was approximately 18%, corresponding to nitrogen leaching as a result of fertilization, while in organic production systems the grey water footprint is zero.
Practices encouraging efficient use of water during a banana plantations’ irrigation process include:
- Calculating irrigation needs based on meteorological data.
- Measuring soil moisture levels. In the plantations of a multinational banana company, it was measured every 15 hectares with five monitoring points to extract samples for analysis, to depths between 0–15 cm and 15–30 cm.
- Applying irrigation based on water infiltration rate, physical conditions of the soil environment, moisture holding capacity, and evapotranspiration.
- Using mulch in thick layers in banana plantations to retain water and reduce evapotranspiration11.
- Use of cover crops with native plants along drainage canals and plantations.
- Using tensiometers to measure the water needs of the plantation. Two tensiometers can be used on a plantation at different points, one at 25 cm and the other at 60 cm. The decision to water is made based on the results of the measurement. In cases of mixed soils or slopes, more tensiometers may be required.
- Training the staff in charge of irrigation on topics such as banana taxonomy, calculation of the water needs of the crop, environmental conditions of the area and their impact on the plantation, distribution of irrigation and proper use of the irrigation system.
- In cases where sprinkler irrigation is used, measuring the amount of water delivered by the spray in different locations of the plantation, to ensure that the same amount of water is provided in the entire plantation. Bear in mind that the sprinklers closest to the pumping station will receive more water than the ones farther apart. In cases where there are significant discrepancies, it is worth considering reducing the distances between sprinklers or reducing the diameter of the pipe.
- In countries like Peru7, where the irrigation system operates by gravity, studies recommend reducing the amount of water used for irrigation and increasing the frequency of watering, which would allow a better use of water in plantations and reduce its consumption.
Packing stations
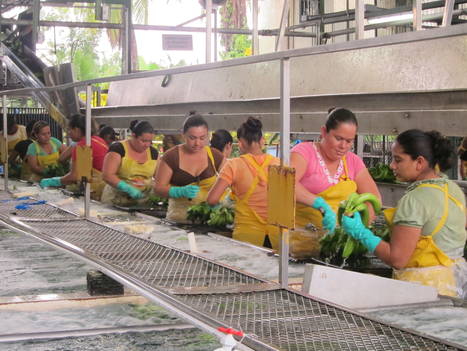
Banana packing stations use water to remove waste, insects and latex from the fruit. Water consumption in packing stations varies depending on the process and water source used.
An analysis conducted in packing stations in Ecuador7, with abundant and low-cost water sources, found that the water footprint is higher than in packing stations in Peru, where there is limited access to water and each packing station pays for the water it consumes. In Ecuador, the calculated water footprint was 576 m3 per tonne – of which, according to the WFN-based assessment, 48% was green water, 34% was blue water and 18% was grey water. In Peru, the calculated water footprint was 599 m3 per tonne, from which 94% was blue water and 6% was green water.
Water saving practices in packing stations
- Banana companies have adopted practices to reduce water consumption in their packing stations7 11, including water recirculation and water quality control to avoid fungus. Some of them implemented water recirculation systems eliminating solids and latex, and added chlorine to the water to allow its reuse for two weeks in the packing process.
- Using less water in the cleaning tanks and frequently monitoring the quality of water discharges – including microbiological analysis and pesticide residue analysis – ensures that reused water complies with the required quality conditions. Samples of water need to be taken for laboratory analysis, with the frequency of these analyses depending on the activity in the packing process of each station.
- Conducting de-handing and de-latexing activities directly in the field and not in the packing stations10.
- Using alum or latex-removal products in the banana cleaning pools allows easy removal of latex and uses less water7.
- Dry dehanding packing stations can also be used.
Results
- Recirculation systems help to reduce water consumption by approximately 80%12. According to a water footprint study including different processing plants11, the water footprint in a packing station without a recirculation system is 1.3 litres per kg of banana, compared with 0.05 litres per kg in a packing station with water recirculation. In the new system, which includes de-handing and de-latexing in the field, the water footprint is 0.02 litres per kg. These amounts are of course very little compared to the amount of water needed for irrigation (around 500 liters per kg).
- Likewise, Costa Rica’s National Banana Association (CORBANA) reported a reduction of 55% in water consumption by implementing water recirculation systems, 23% by reducing water depth in the cleaning pools, and of 19% by using additional products to clean the cleaning pool water13.
References
References
1 FAO; Earthscan. 2011. The state of the world's land and water resources for food and agriculture
2 Roibás, L. Elbehri, A. & Hospido, A. 2015. Evaluating the sustainability of Ecuador bananas: Carbon footprint, water usage and wealth distribution along the supply chain
3 Water Footprint Network. What is a water footprint?
3 HIDROCEC-UNA. Aplicación del cálculo de huella hídrica para regiones de cultivos de café, bananao y arroz en Costa Rica
4 Ana Lorena Vallejo. 2015. Metodología práctica para la cuantificación de la huella de agua en Plantas Empacadoras de banano en Costa Rica” Ana Lorena Vallejo Chaverri
5 Hoekstra, A., Chapagain, A., Aldaya, M. & Mekonnen, M. 2011. The water footprint assessment manual
6 Mekonnen, M. & Hoekstra, A. 2011. The green, blue and grey water footprint of crops and derived crop products
6 Water Footprint Network. Product gallery
7 Zarate, E; Kuiper, D. 2013. Water Footprint Assessment of Bananas Produced by Small Banana Producers in Peru and Ecuador
8 AUGURA. 2009. Buenas prácticas agrícolas en el cultivo de banano en la región del Magdalena
9 University of Victoria. 2002. The Ecological footprint of a Dole Banana
10 Soil & More International. 2011. Water Footprint Assessment Bananas and Pineapples Dole Food Company
11 LimnoTech. 2012. Water Footprint Assessment Banana and Lettuce Products Produced by Chiquita
12 Chiquita Brands International, 2012. Corporate Social Responsibility Report
13 CORBANA. 2013. Planificación e investigación para ahorrar agua en la industria bananera